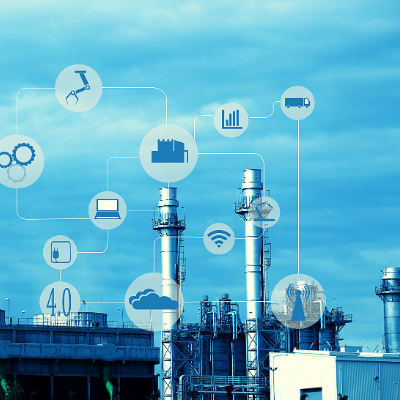
La 4e Révolution Industrielle a pour principal enjeu la création d’usines intelligentes permettant une interaction continue entre les machines et les utilisateurs et la prise en compte des données pour adapter les processus productifs aux réalités commerciales et techniques.
Cette évolution vers une industrie 4.0 offre de nouvelles opportunités aux entreprises suisses, notamment grâce à une intégration flexible des clients et une augmentation significative de la qualité et de l’efficacité de la production (DELOITTE).
Dans le domaine du dépannage et de la maintenance, la mise en place de stratégies de maintenance prédictive représente l’un des bénéfices attendus de cette numérisation de l’industrie. Selon une étude allemande, une entreprise sur trois aurait déjà mis en œuvre des projets de ce type outre-Rhin en 2021 (bearingpoint, 2021).
Tout comme la maintenance préventive, la maintenance prédictive vise à contrôler les outils de production afin d’anticiper les problèmes pour les corriger à temps. La différence entre ces deux concepts réside dans le fait que la maintenance prédictive se base sur l’utilisation des données historiques et des données en temps réel pour anticiper les problèmes avant qu’ils ne surviennent. Elle permet ainsi de réduire la fréquence de maintenance et les temps d’arrêt par des interventions mineures ne nécessitant idéalement pas d’arrêt des processus de production et corrigeant les problèmes avant qu’ils ne soient trop importants.
La mise en place d’une stratégie de maintenance prédictive
Pour garantir le succès d’une telle stratégie de maintenance, les entreprises doivent suivre certaines étapes essentielles à sa mise en place :
- La fixation de l’objectif : Il s’agit de définir de façon précise sur quels actifs vont porter la prédiction. Ces actifs peuvent être tout type d’installations industrielles, telles que des pompes, des moteurs, des systèmes électriques, … Cette étape vise entre autres à établir des indicateurs permettant de mesurer la rentabilité de la stratégie de maintenance prédictive.
- La collecte de données : L’idée est de prédire quand une anomalie doit arriver à partir d’une analyse de données historiques et actuelles. L’installation de capteurs et de systèmes de surveillance va permettre de collecter et de stocker des données en temps réel sur les performances et la bonne santé des équipements.
- L’extraction d’informations : Elle consiste à interpréter les données collectées et à les renseigner dans un système de planification et d’optimisation automatisé pour qu’elles puissent être exploitées. Des logiciels de gestion de bases de données combinés à de l’intelligence artificielle sont en mesure de faciliter ce processus. Le but est de croiser et d’analyser les données pour identifier les signaux précurseurs de défaillance ou de problèmes potentiels et en tirer des conclusions utiles.
La mise en place d’alertes et de notifications : Les systèmes d’alerte et de notification émettent des avertissements en cas de conditions anormales ou de défaillances imminentes. Ceci aide les utilisateurs à agir rapidement en cas de besoin d’ajustement ou de remplacement de pièces et à planifier des interventions de maintenance de manière proactive.
Les méthodes de surveillance de la maintenance prédictive
Pour couvrir efficacement les équipements, la maintenance prédictive se base principalement sur des équipements dotés de capteurs reliés à internet (Internet of Things – IoT) et doit donc pouvoir effectuer certaines analyses, telles que :
- L’analyse des vibrations : Cette méthode consiste à mesurer les vibrations des équipements à l’aide de capteurs spécifiques. Les variations anormales dans les niveaux de vibrations peuvent indiquer des problèmes de désalignement, d’arbre tordu, de composants déséquilibrés, de composants mécaniques desserrés, etc. L’analyse des vibrations est parfaite pour les équipements et machines rotatifs, tels que les compresseurs, les pompes à eau et les moteurs.
- L’analyse des ultrasons : La plupart des machines produisent des ondes sonores pendant leur fonctionnement, même si elles ne sont pas détectées par l’oreille humaine. Grâce à des capteurs qui transforment les sons en données audios ou numériques, des défaillances de systèmes électriques, de valves et des fuites de gaz peuvent être détectées. Cette technique est principalement utilisée pour les canalisations transportant des liquides ou du gaz.
- L’analyse infrarouge ou l’imagerie thermique : Elle sert notamment à mesurer, grâce à la lumière, les variations de température des équipements électriques et mécaniques (roulements, moteurs électriques, etc.) et à détecter l’usure, la rouille ou encore les déconnexions difficilement visibles à l’œil nu. En effet, les éléments d’équipement usés, y compris les circuits électriques défectueux, émettent généralement de la chaleur qui s’affiche sous la forme d’un point chaud sur une image thermique. Les techniciens peuvent ainsi intervenir efficacement et éviter les pannes d’équipement et même les gros accidents. Cette technologie de contrôle non destructif est considérée comme l’une des technologies de maintenance prédictive les plus polyvalentes. Elle peut être utilisée pour analyser tout, des pièces individuelles des machines aux systèmes d’usine et même des installations entières.
Il existe de nombreuses autres méthodes permettant la mise en évidence automatisée de dysfonctionnements ou de prémisses de dysfonctionnements, telles que l’analyse des niveaux de fluide et l’analyse des données d’exploitation.
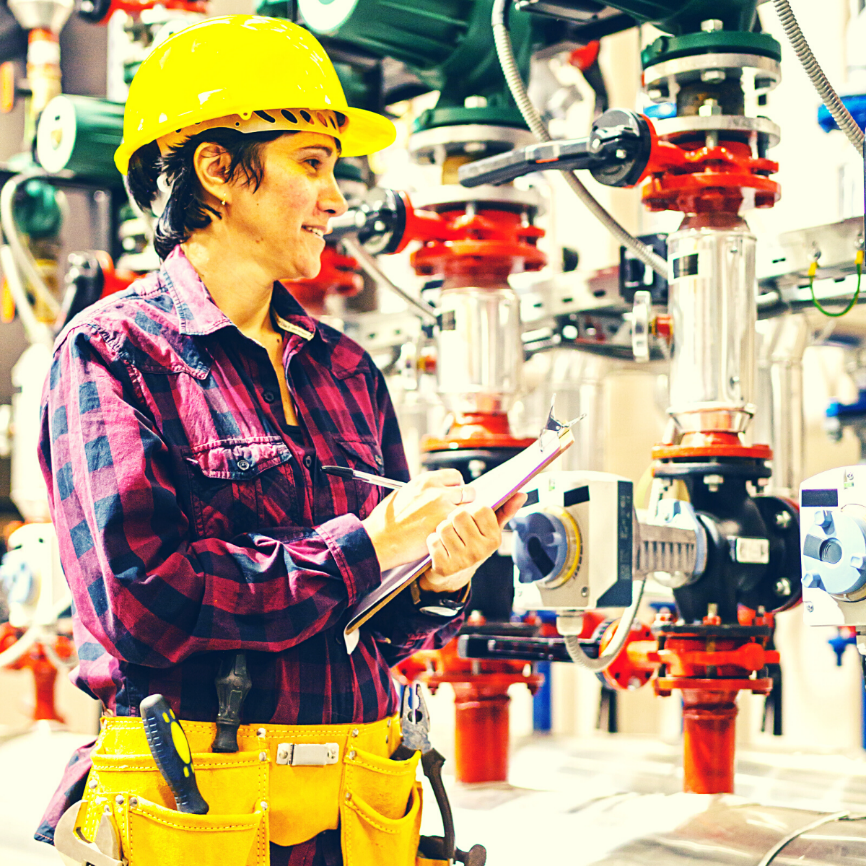
Les avantages de la maintenance prédictive
Comme tous les concepts de maintenance, la maintenance prédictive, constitue une solution pour allonger la durée de vie des équipements et accroître leur retour sur investissement (consultez notre article à ce sujet pour plus de détails).
En planifiant la maintenance des objets sans arrêter le processus de production, la maintenance prédictive permet aux entreprises industrielles ou agricoles d’optimiser leur temps de fonctionnement en minimisant le nombre d’heures perdues sur des opérations de maintenance préventive.
Elle a également pour avantage de réduire certains coûts liés au changement total ou partiel de l’équipement en détectant les pannes avant qu’elles ne surviennent et en évitant le changement de pièces ou composants onéreux. La maintenance prédictive permet aussi la mesure des interactions entre installations pour déterminer les actions de maintenance à entreprendre afin d’augmenter la productivité globale de tout un site de production. Cette hausse de productivité serait évaluée à 25%, la réduction des coûts de maintenance à 25% et la réduction des temps d’arrêts à 70% (DELOITE).
Les limites de la maintenance prédictive
Bien que les estimations les plus optimistes indiquent que la maintenance prédictive puisse entraîner une multiplication par 10 du retour sur investissement des installations (fiixsoftware), les coûts liés à la mise en place d’une telle stratégie freinent beaucoup d’entreprises industrielles et agricoles. En effet, en plus des coûts de démarrage très élevés (ex : installation de capteurs, remplacement d’installations incompatibles, mise en réseaux et installation de logiciels…), les entreprises doivent se doter de personnels compétents et donc capables d’analyser efficacement les données présentées. D’autre part, la maintenance prédictive ne fait généralement que constater l’existence d’un problème et ne notifie pas toujours aux utilisateurs les actions à entreprendre.
Les outils de maintenance prédictive peuvent aussi conduire à des erreurs d’évaluation, car certains facteurs tels que l’âge de l’équipement ou des facteurs externes comme la météo qui influe sur la température des installations peuvent ne pas être pris en compte dans les modèles.
Notons également que la maintenance prédictive repose sur la collecte et l’analyse de grandes quantités de données. Pour obtenir des résultats précis, il est essentiel que ces données soient de haute qualité et représentatives de l’état réel des équipements. Cela peut poser des défis dans les cas où les données historiques sont insuffisantes ou de mauvaise qualité, ce qui limite l’efficacité de ce type de maintenance.
Conclusion
En somme, cette technologie peut constituer un véritable avantage compétitif, pour autant que l’entreprise aie clairement déterminé ses objectifs et dispose des ressources et compétences nécessaires à sa mise en œuvre. Avant de mettre en place un concept de maintenance prédictive, une étude approfondie menée par des experts est donc nécessaire, afin de déterminer si cette méthode apporte une réelle plus-value à l’entreprise concernée.
Retrouvez chez ST Solutions, des experts qualifiés pour vous conseiller et vous accompagner dans la mise en place de votre stratégie de maintenance prédictive.
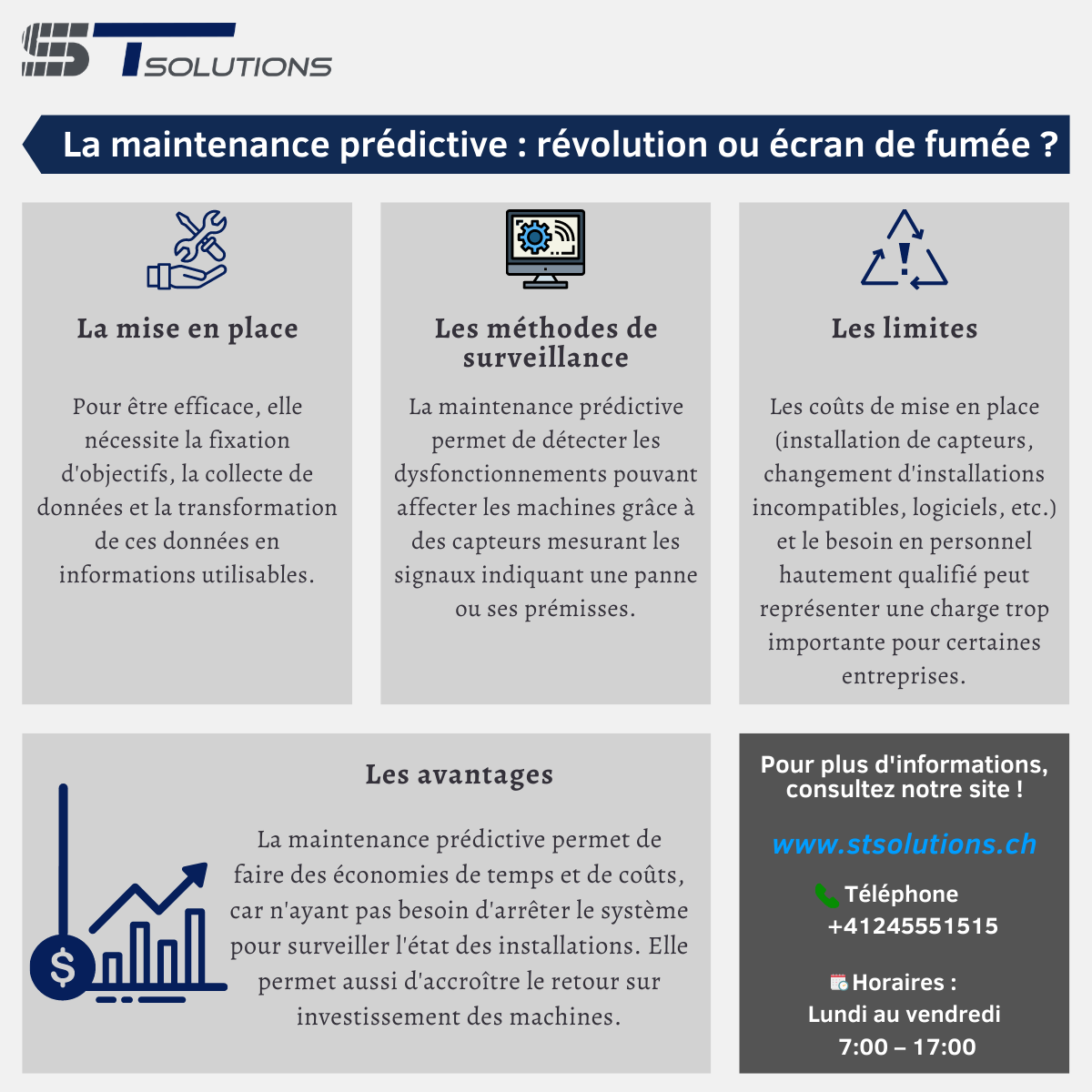
Commentaires récents